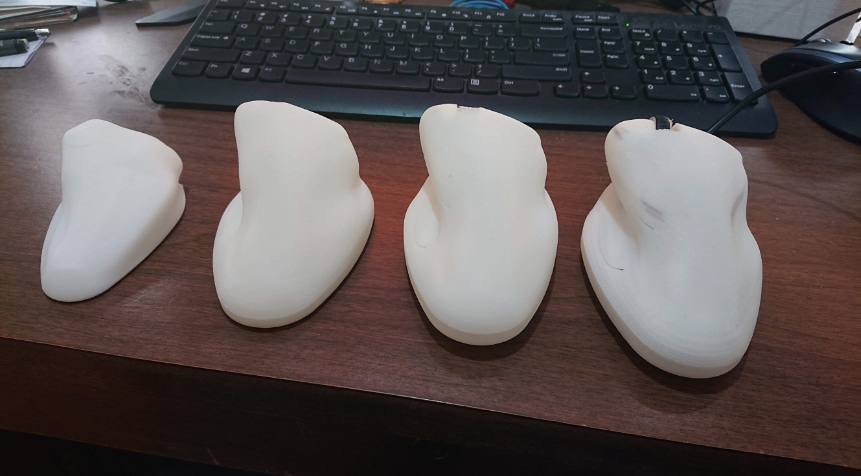
The Challenge
Develop a Unique Form that can be Quickly Made and Quickly Tested.
Using my Industrial Design background, I took this challenge as a chance to go through the full form development process when designing a physical element for for user testing. Beginning with rough sketching and ending with interactive rapid prototypes.
Skills Used: Sketching, Foam Modeling, Laser Cutting, 3D modeling, 3D printing, Design for Manufacture, Arduino Integration
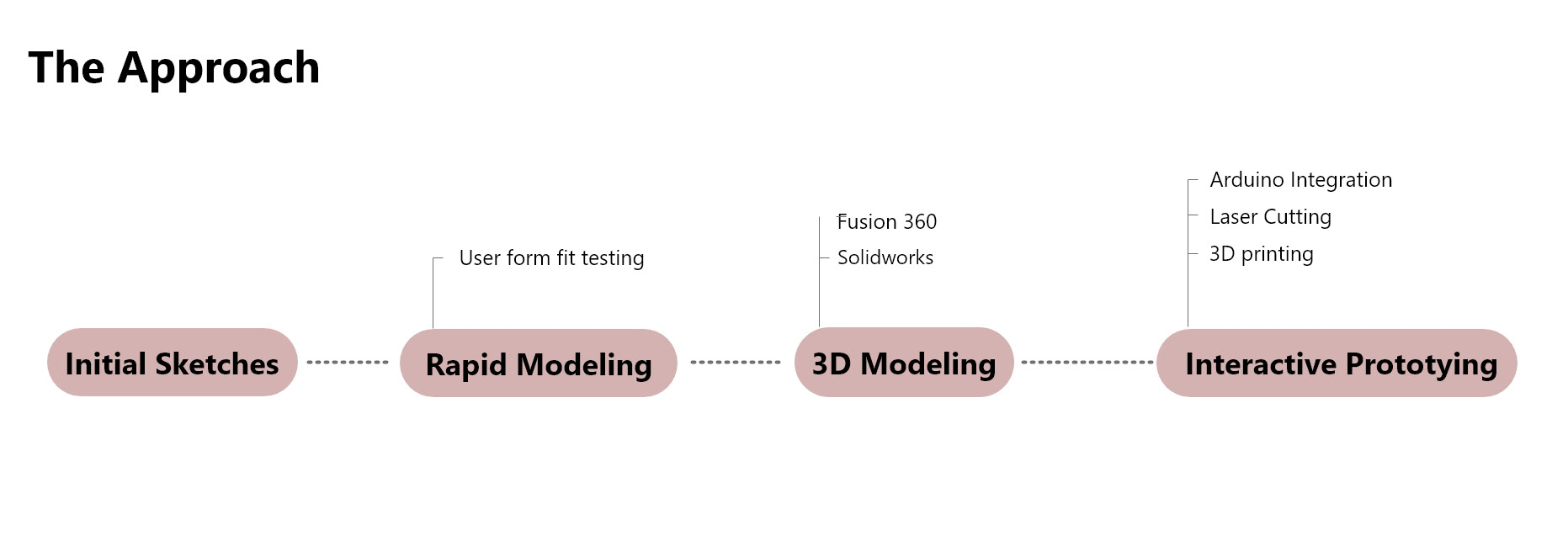
Initial Sketches
I initially chose to redesign a computer mouse in order to take the opportunity to see if I could make a unique design and unique interaction for a heavily designed product.
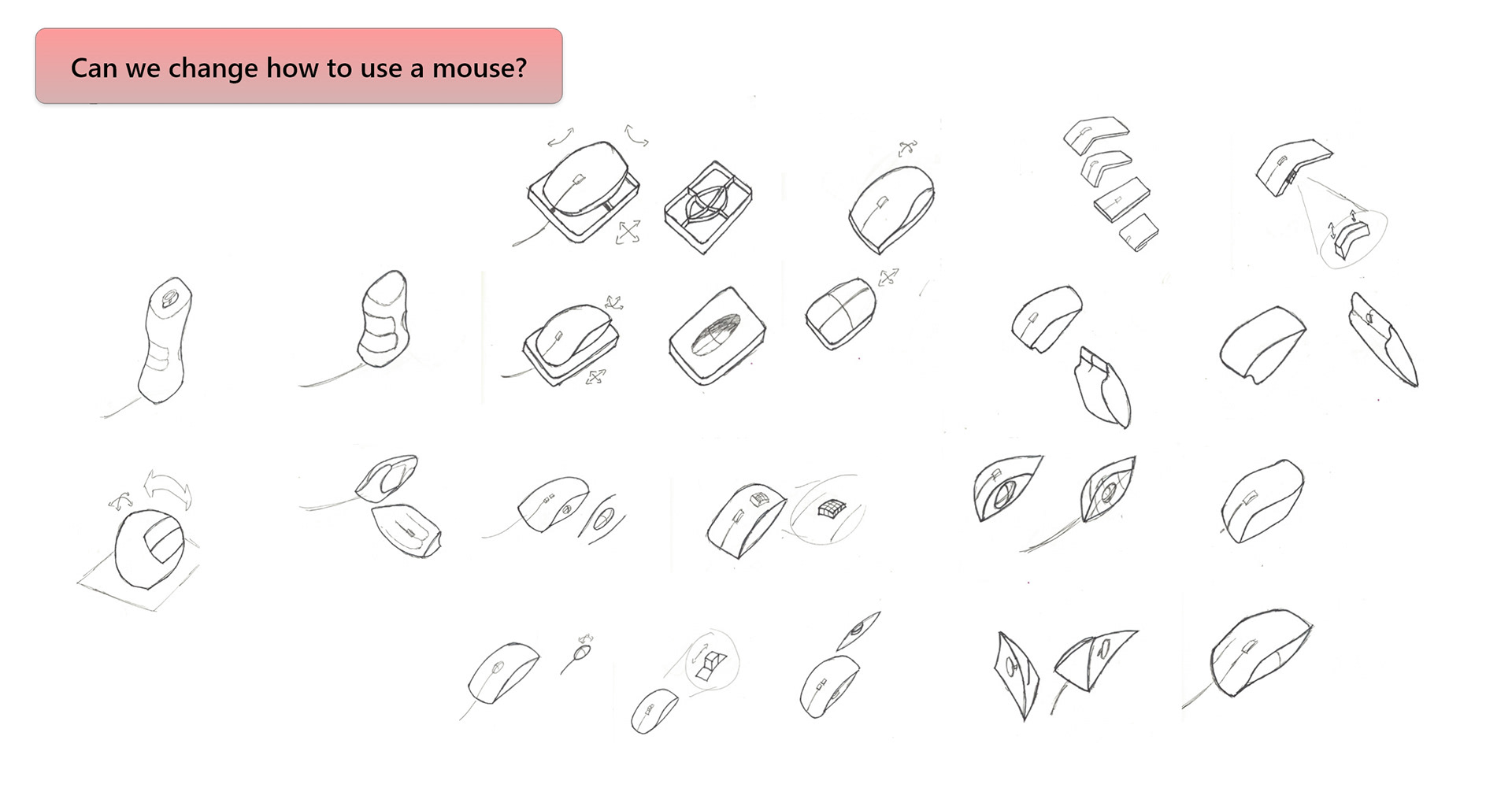
Final Concept
Looking through my sketches, I became inspired by the undergrip concepts. Through my research I was not able to find much like this on the market and wanted to see if I could make this form work, or learn why this form doesn't work.
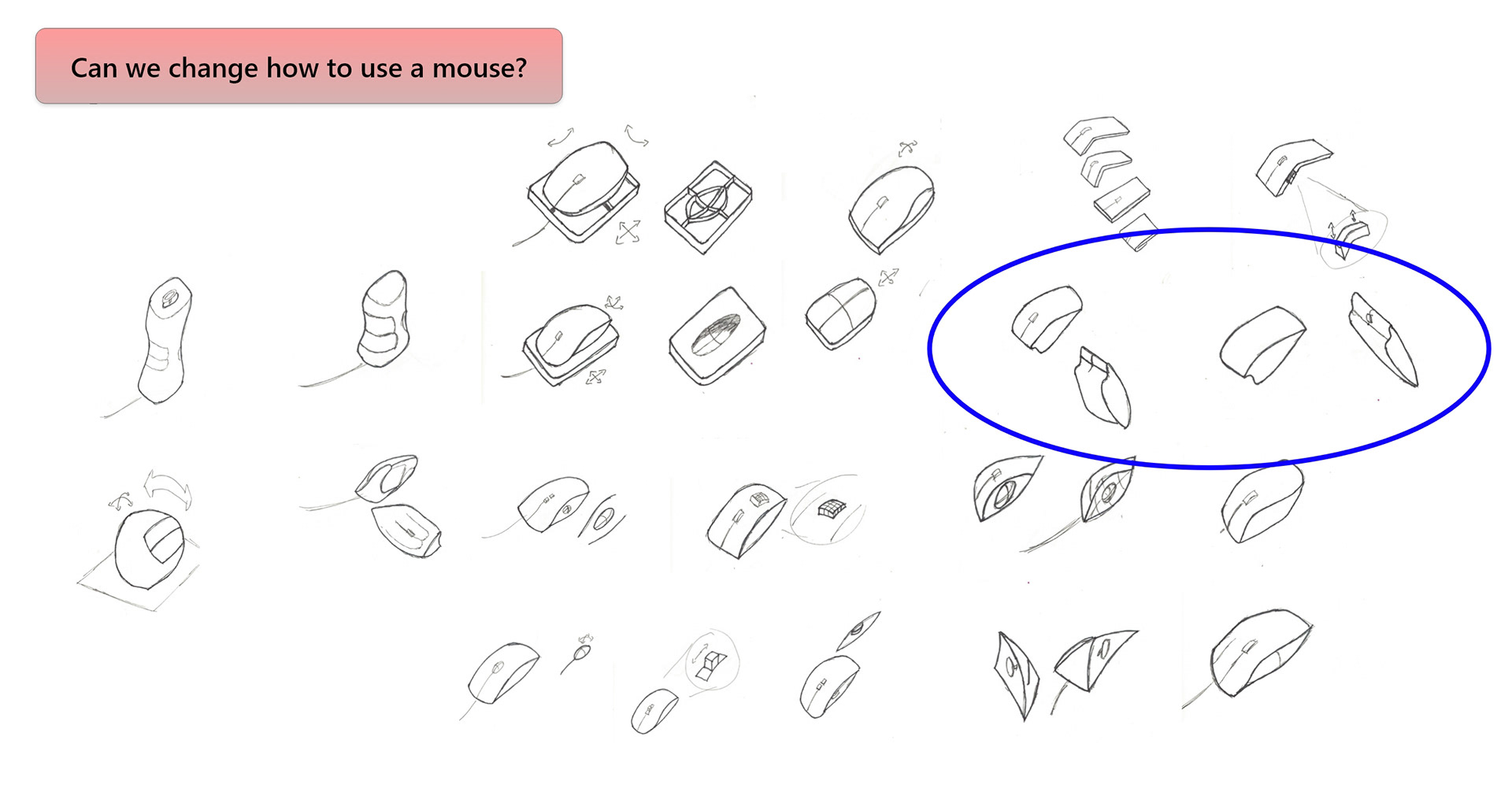
Rapid Modeling
Foam Modeling
Making a series of foam models, I quickly discovered my initial concept for the form was entirely uncomfortable for a user, however through each iteration, taking each form to different users to grip, I was able to find a comfortable form that was operated through undergrip buttons interaction.
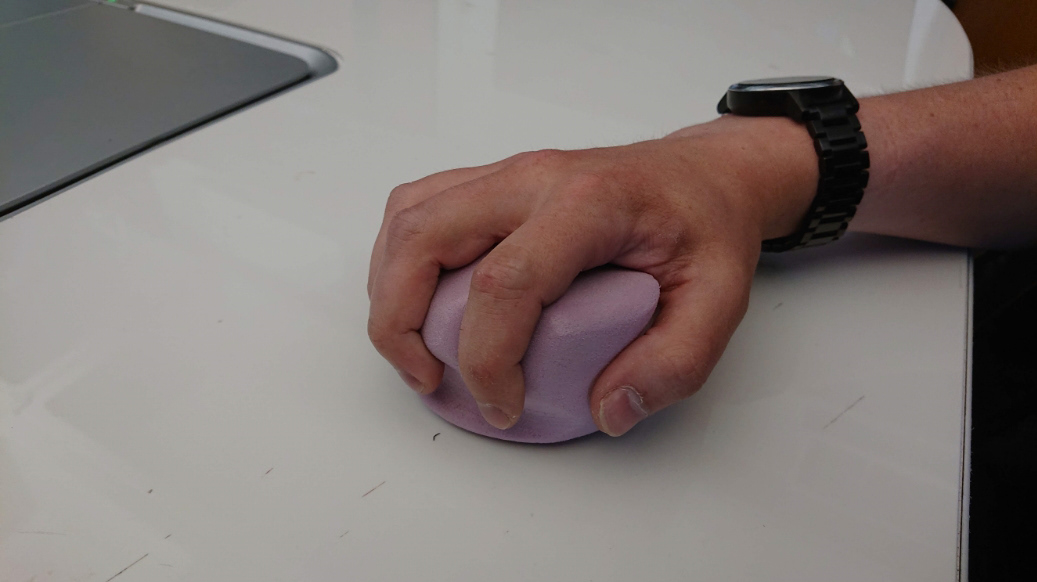
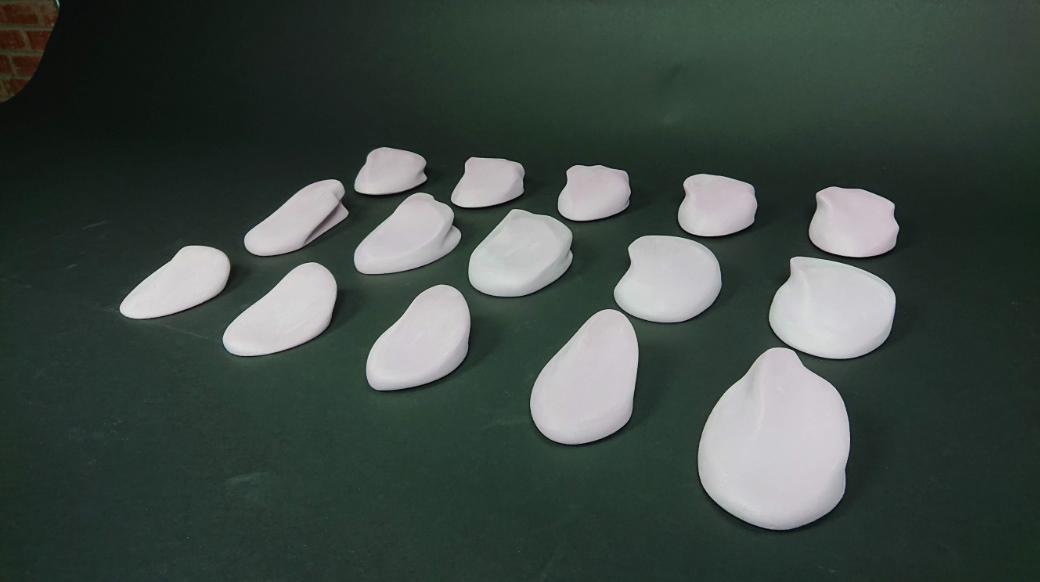
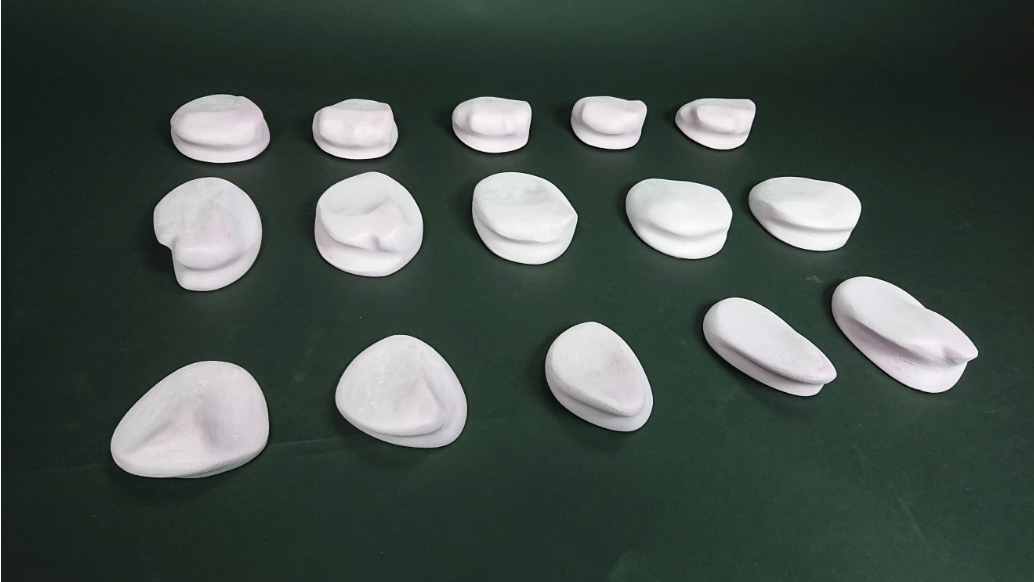
3D Modeling
Fusion 360 Modeling
The next step was creating a construction drawing set of the foam model and creating a model in Fusion 360 for more minor changes and experimenting with color. Due to such an organic form, this did involve some deviation from the foam model form that would need to be tested again for a final confirmation.
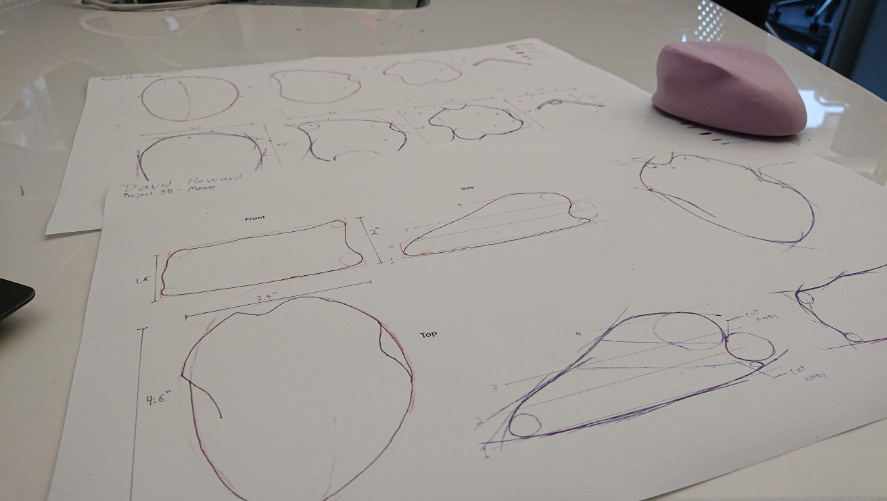
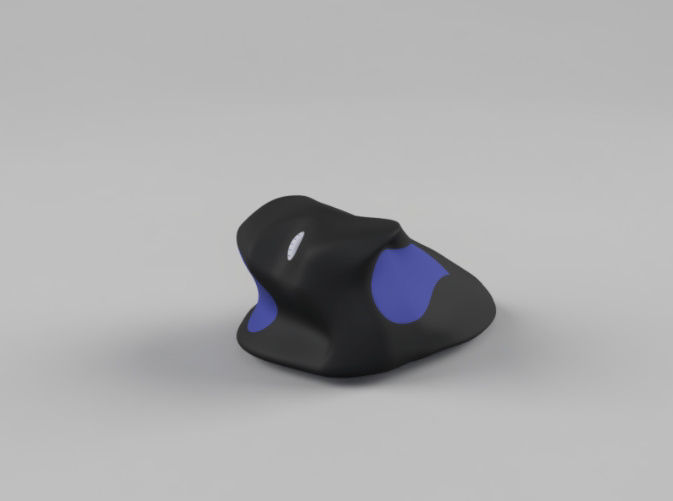
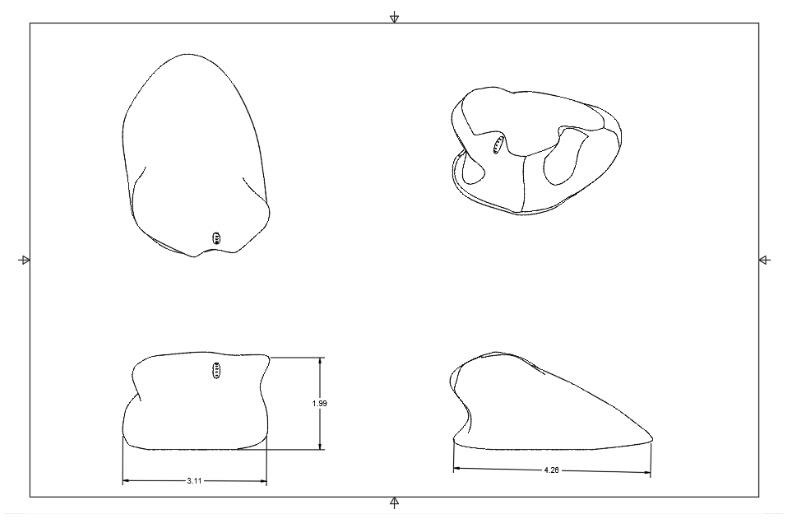
Stacked Lasercut Test
In order to test this model, I then sliced a solidworks form of the model into laser cuttable sections. These sections were easily stackable and cut from cardboard to quickly test sizings again.
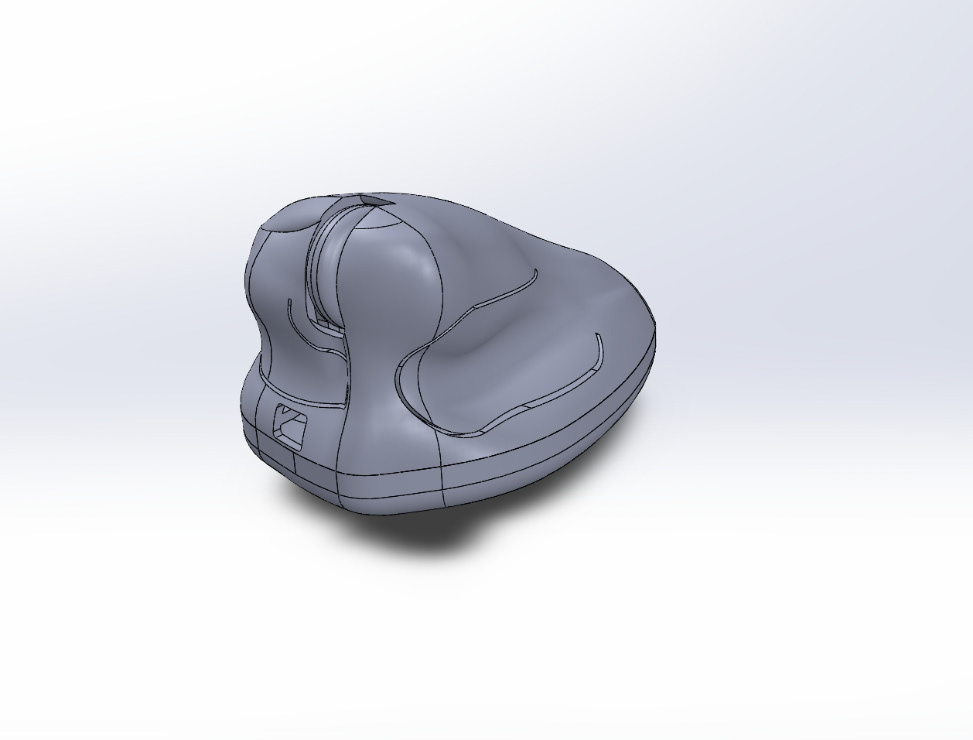
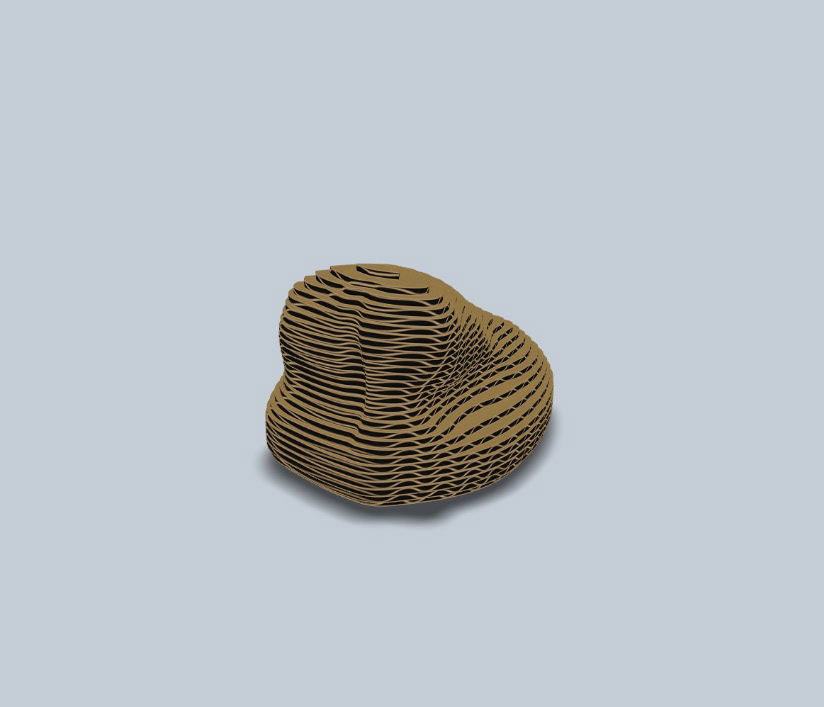
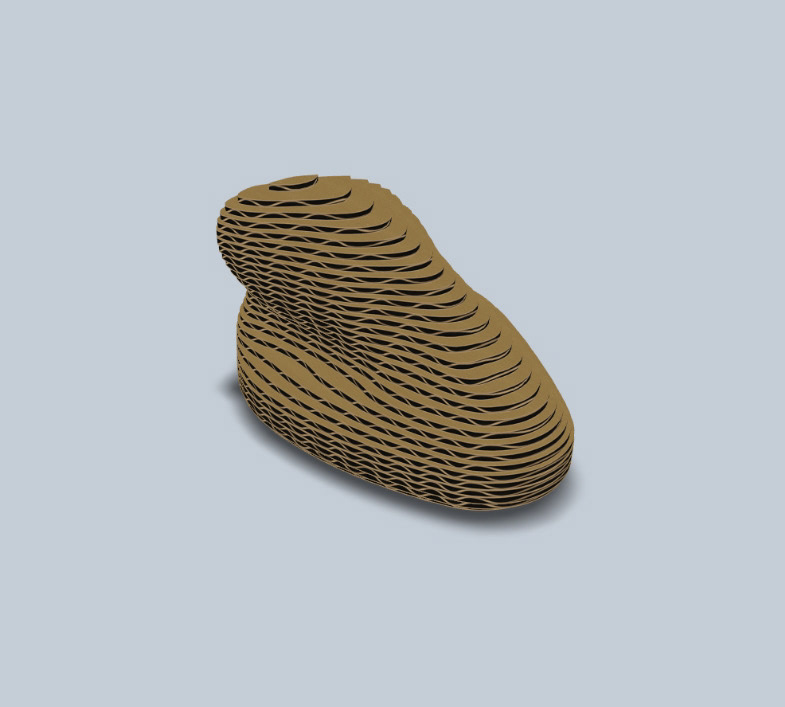
Interactive Prototyping
3D Printing
From this model, I then began 3D printing. Initially I was printing for the exterior of the model to completely ensure a good fit and that my printing process was giving the intended outcome. These models were all printed using an FDM style of printer to cut down on costs at this stage of a process.
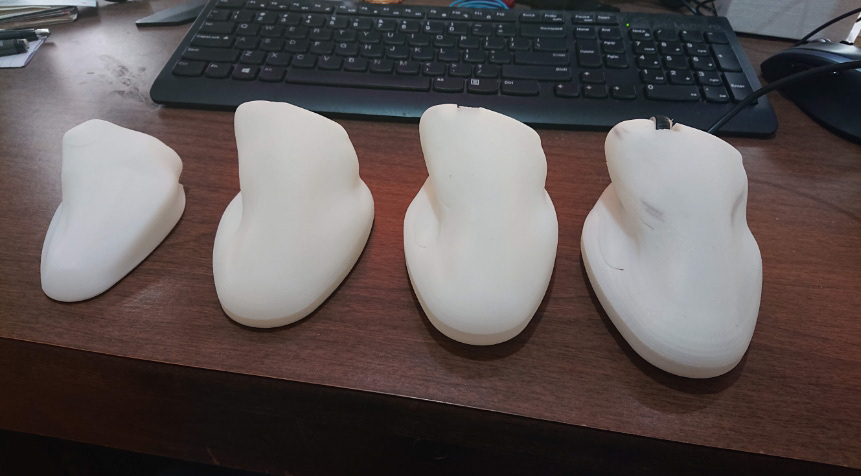
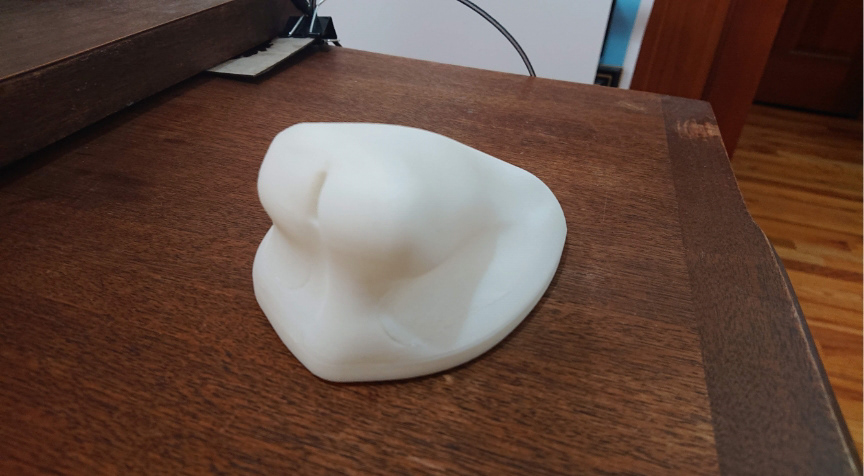
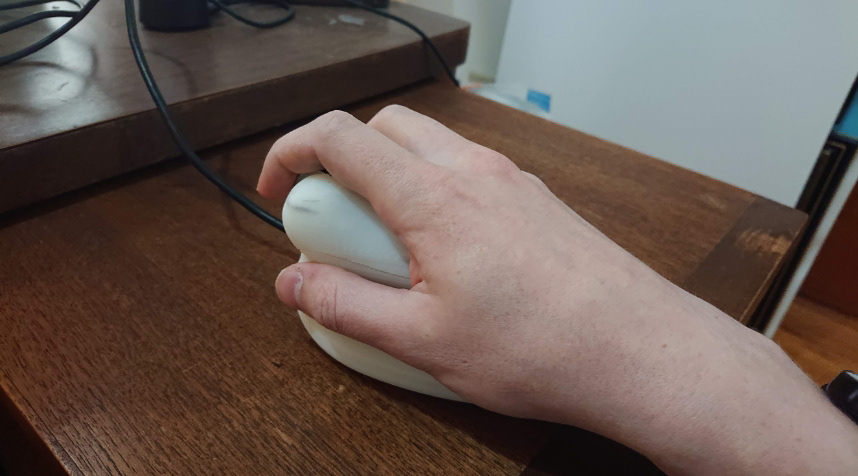
Integrating Electronics
Using a circuit playground, buttons, and a scrollwheel from an existing mouse, I then designed the interior to house these components and quickly created code that could give feedback to a user.
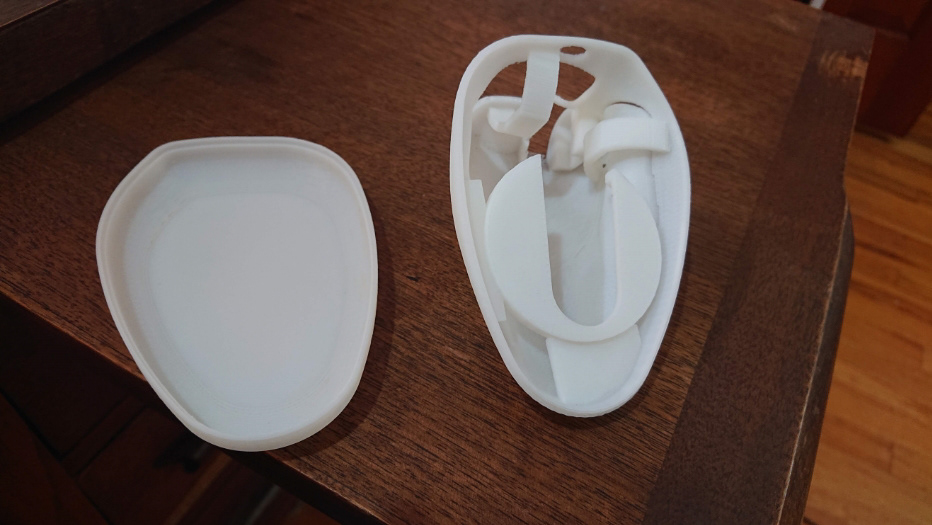
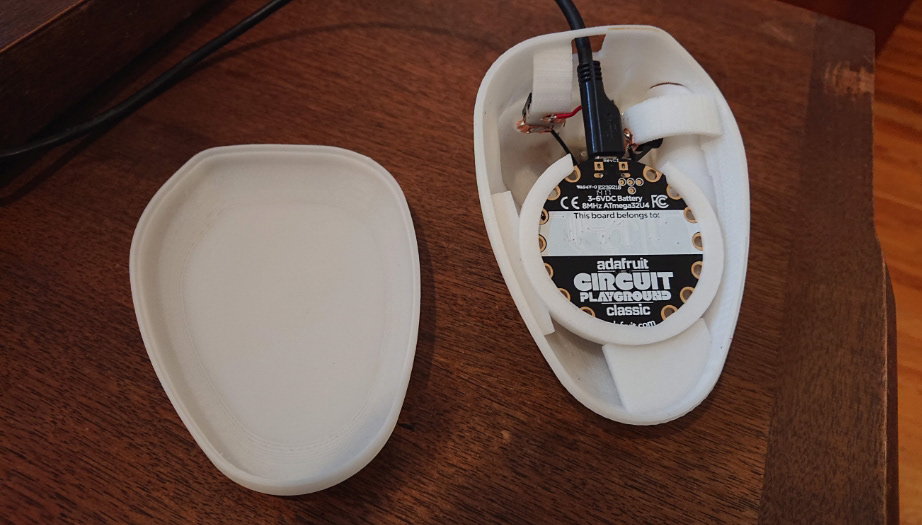
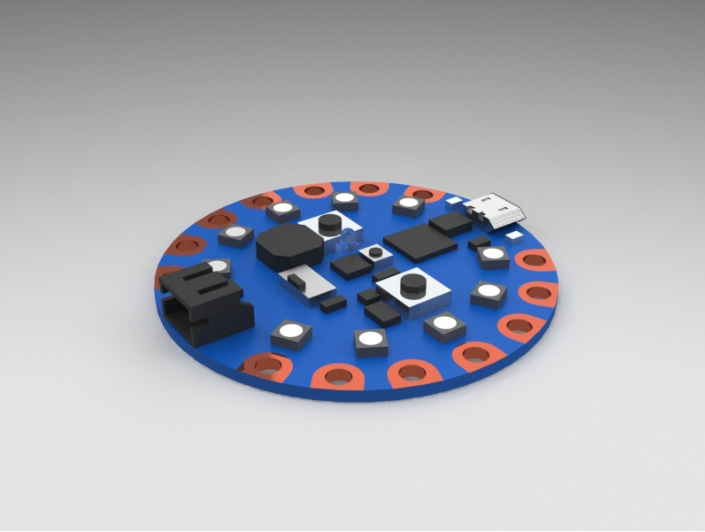
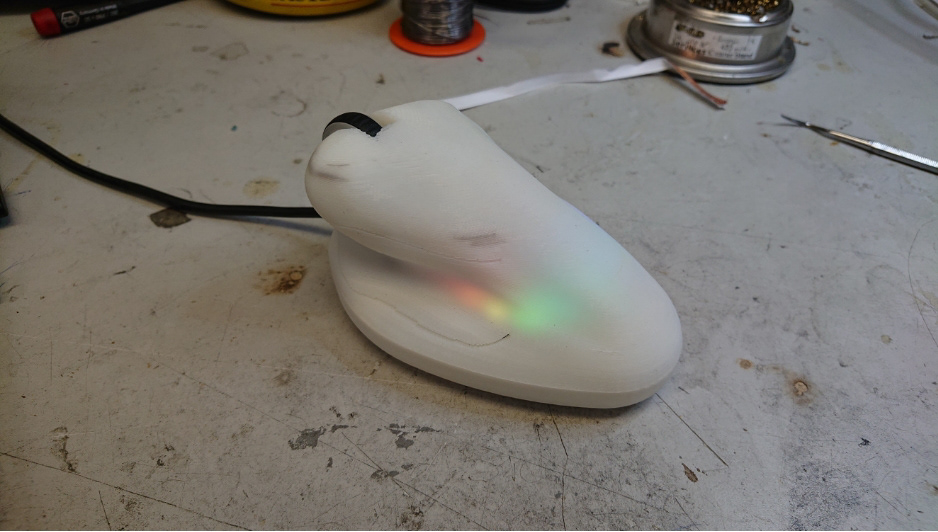
Final Prototype
My final model was a fully functional mouse that could be tested by users. I added LED feedback as well for the users since the circuit already included some and I could easily add another sense to design for.
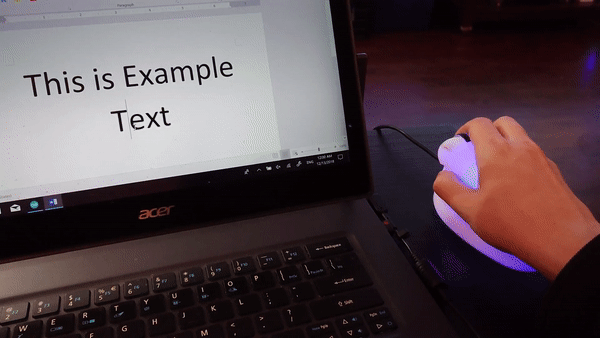
Conclusion
This project felt like a great mix of my ID training and the user testing experience I have gained through HCI. While I always enjoy this kind of work and would love to continue developing this kind of project, there was no need to go further. I was able to create a completely testable prototype and gained enough feedback to create a result.
While users initially were skeptical when looking at the form, most users actually enjoyed using the mouse once they gripped it. It was an interesting observation that while the form is acceptable, without some kind of ergonomic study, it is too strong of a break from the mental model of a mouse to go into the market. This is unfortunate, but an important finding if I wanted to take something like this further.