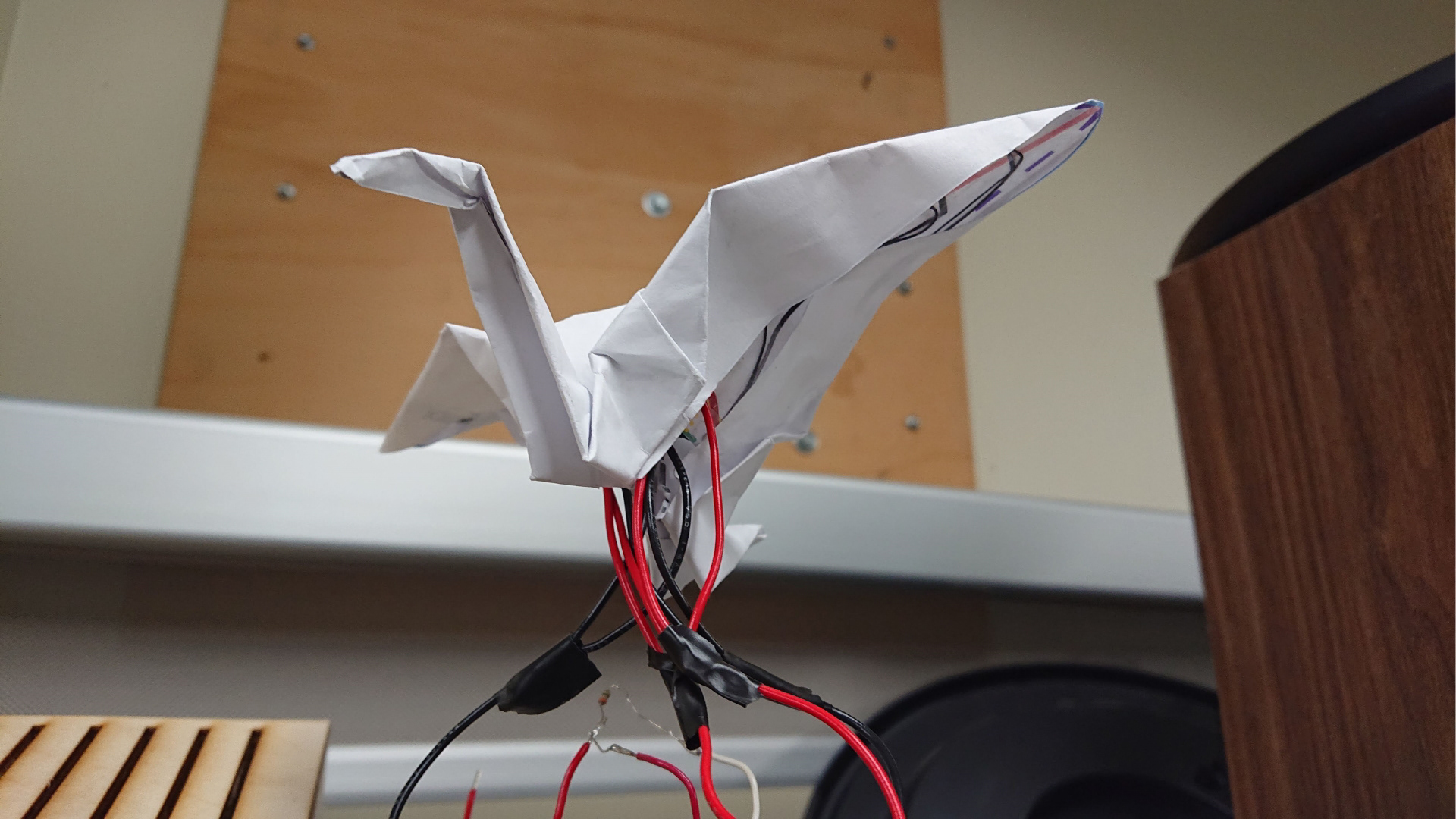
The Challenge
How might we create a delightful, tactile interaction through Origami?
"Understand an expert, and implement an digital intervention in their craft without disrupting it." This was my challenge going into this project. I chose to follow my interest in paper folding and performed an ethnographic study and design proposal in this field. I interviewed and observed an origami expert, and chose to add a tactile interaction to his craft that would be unique to his interests and skills. My final proposal was a set of instructions of adding Shape Memory material to his paper folding, creating motion in his already organic pieces. Despite not being the expert of this craft, I did attempt to create a high fidelity prototype that might be able to prove the concept as well as inspire the expert as well.
Skills Used: Interaction Design, Ethnographic Research, Physical Prototyping, Electronics Prototyping, Design for an Expert, Arduino Prototyping
Read the full case study and design process here!
Concepting
Initial Concepts
To begin my concepting phase, I created a rough set of guidelines to give me something to aim towards moving forward. As I was brainstorming, I noticed that I was gravitating towards experimenting with paper as a medium.
Perhaps the qualities of the paper could change the result of the piece?
Not having a single direction, but many possibilities, I created different types of prototypes, experimenting with paper as a medium and the digital possibilities associated with it. Thinking back to Akhil, with a background in Electrical Engineering, incorporating some kind of electronic component makes sense, and could make this product unique to him among origami experts.
Concept: Zap
Zap was an experimenting with treating the paper as part of a circuit. Made using conductive fabric adhered to paper, this prototype treated the entire form as a wire within a larger circuit.
This concept also lent itself to being developed further with a more complex circuit pattern. Can the function of the circuit change based on the form of the product?
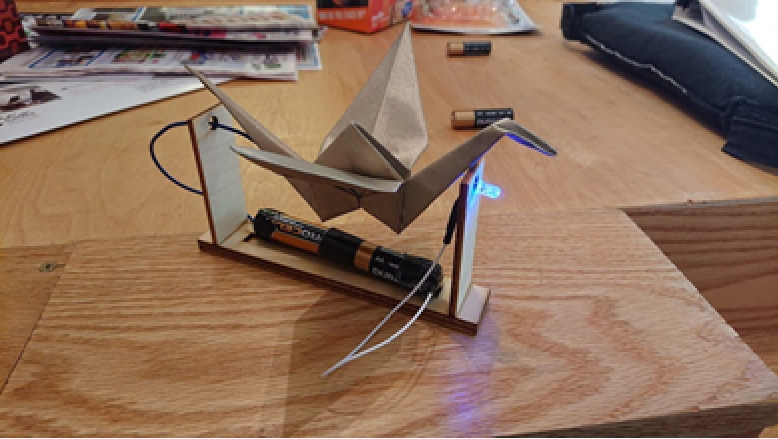

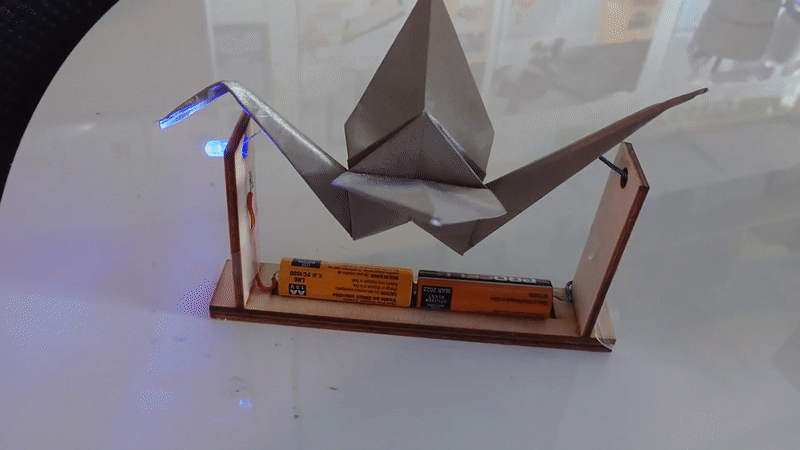
Concept Zap2
I then looked at paper as a resistor within a circuit. Made with applying spray nickel to paper, this 1mOhm form could be used as a capacitive sensor when attached to a micro-controller.
This concept also has future applications with the form having a huge effect on the sensor value. Can each product be a unique interaction based on minor changes within the form?
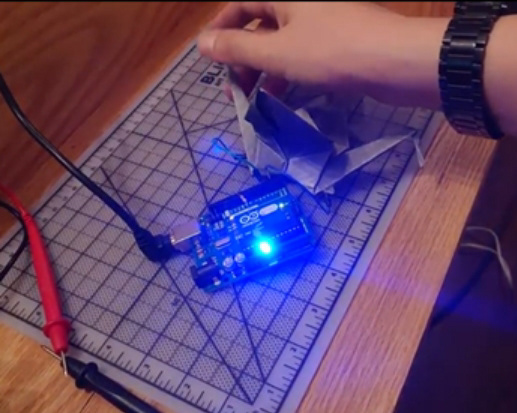
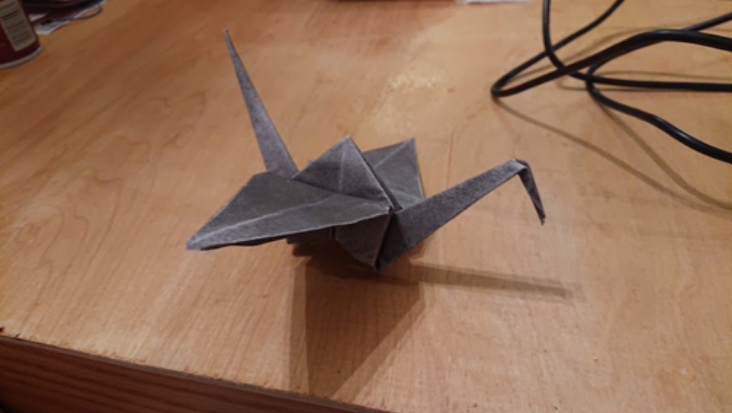
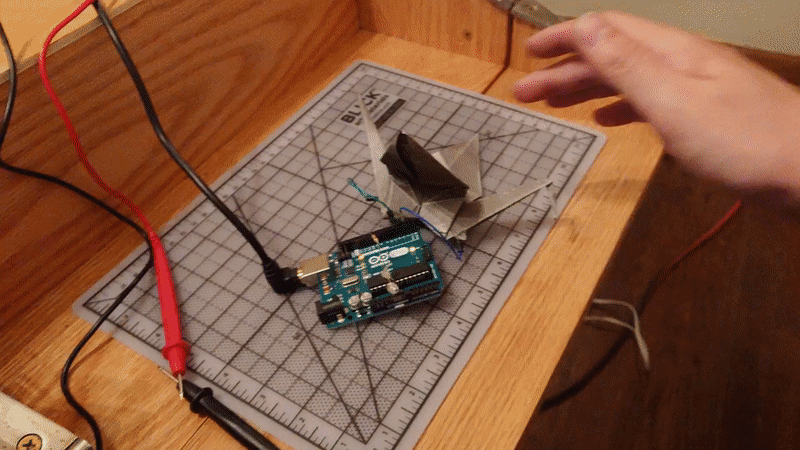
Concept Molt
Finally, I looked at creating taking the concept of action origami a step further. Doing some research into SMA materials, I was curious of the possibilities of applying to paper and create motion with the pieces. This could also create a natural movement of his nature related pieces. Due to the turnaround time, I was only able to make sketches of the possibilities rather than prototyping them.
This concept also has future applications with interaction. Can motion be responsive to some kind of human interaction?
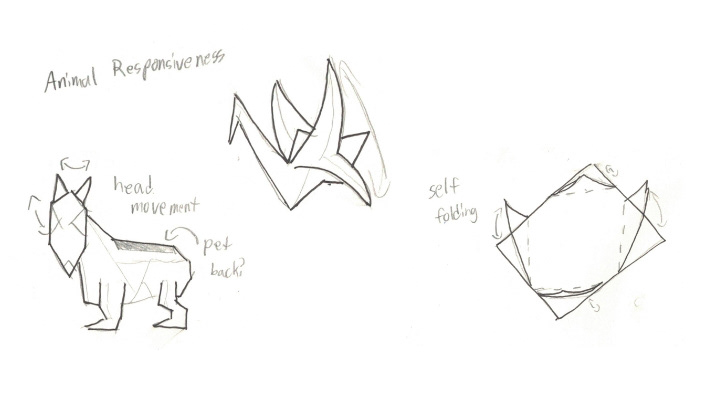
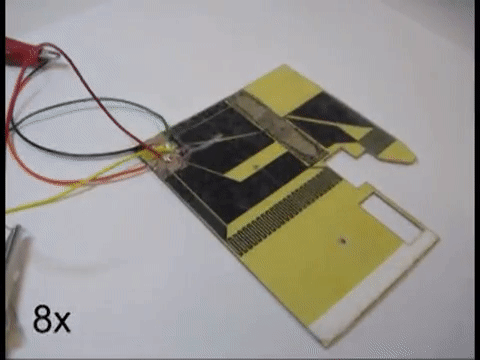
Final Concept
Ultimately, despite not having a prototype, the motion origami was the most inspiring concept that was also feasible to complete within the time limit of the project. The final concept would be a paper crane that flaps its wings in response to touching its neck.
While the conductive paper approaches were incredibly interesting, I ultimately had to consider my own skill set and time as well. While I was confident these were possible, I could not feasibly complete a proper prototype or design with my current skill sets and will save them for a later passion project.
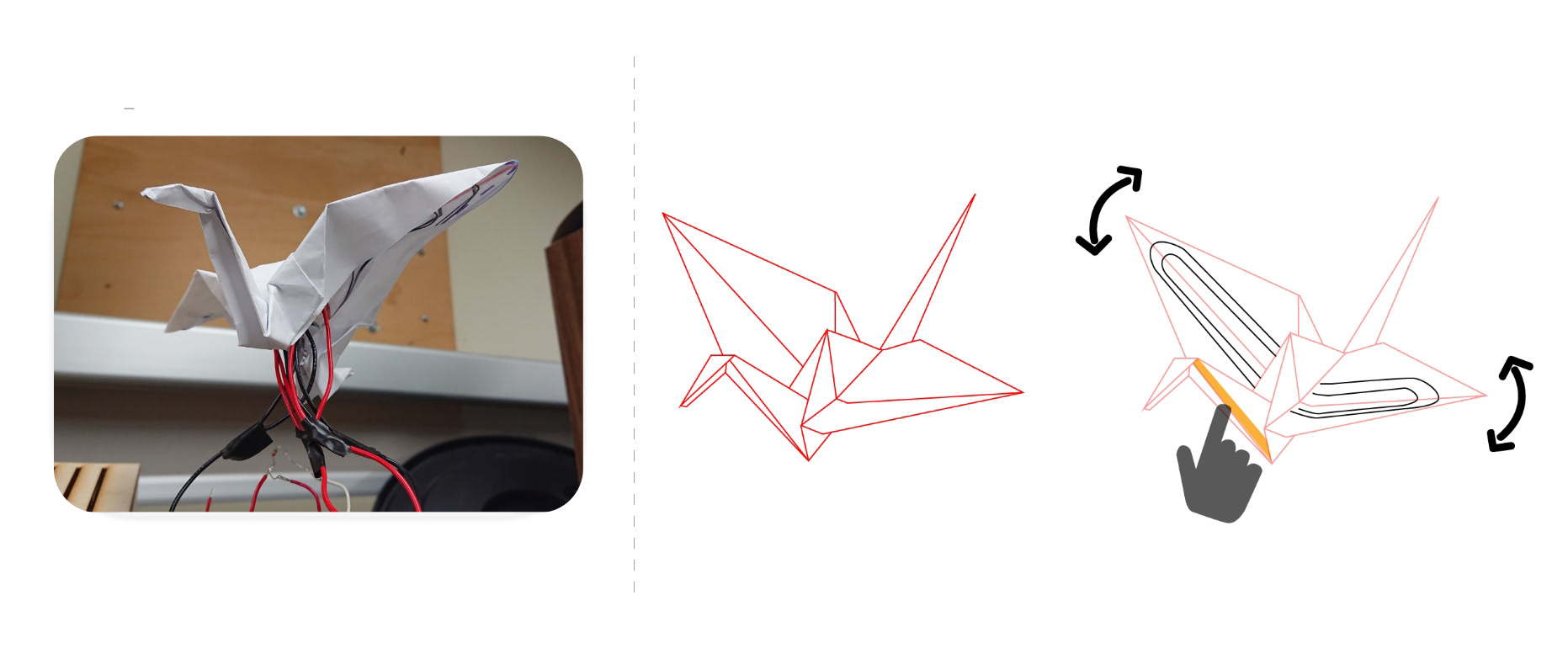
Prototyping
Technology
Thinking of the project timeline, I decided that I could explore the possibilities of the animation concept the most by creating a high fidelity prototype. However, this was not a technology I was familiar with, nor was it incredibly well documented. I knew that I would need to quickly make many iterations and learn quickly from each one.
Despite being the feasible approach, this prototype would require a lot of learning and inventing very quickly. To begin, I started looking at different ways to apply SMA wire and integrating it into the form of a paper crane. There are a surprisingly large amount of methods to apply SMA materials to paper, however, through quick trial and error, I was able to find a balance between wire, strength, thickness, and heat needed.
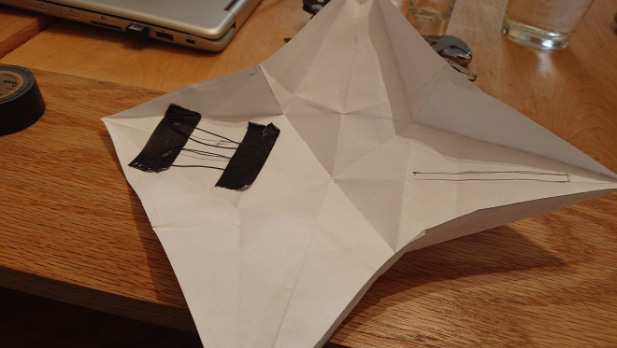
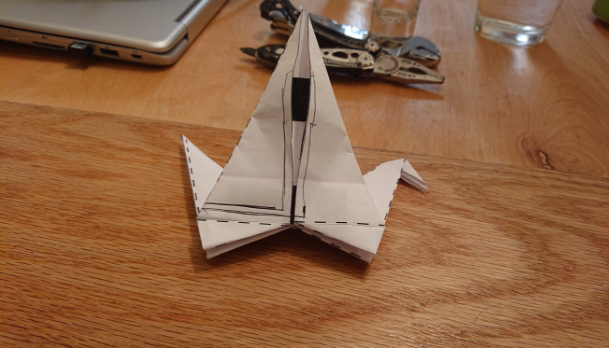
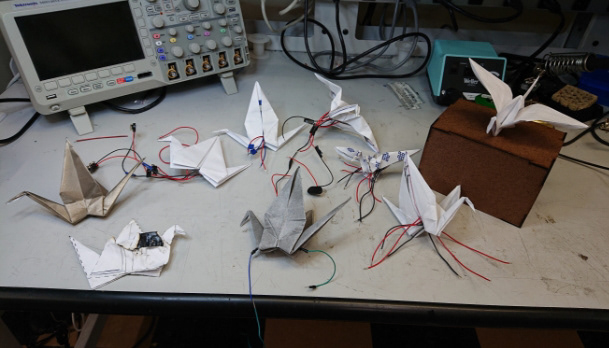
Next, I quickly learned that there were several methods to program the wire, however, there was not a good method to get a consistent programming with he tools I had on me. Programming the wire involves heating it to around 900F, however, the wire will actively move when heating, requiring a custom jig that did not absorb too much heat from the wire. Eventually, I was able to create a method inspired by pipe bending. While it is still not perfectly uniform, these imperfections, actually help create the natural like qualities when applied correctly.
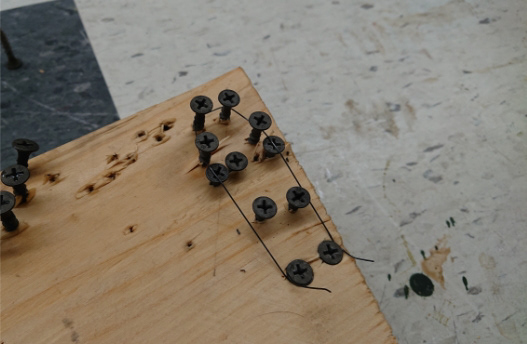
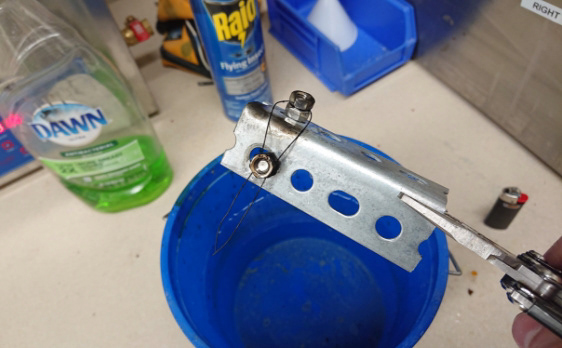
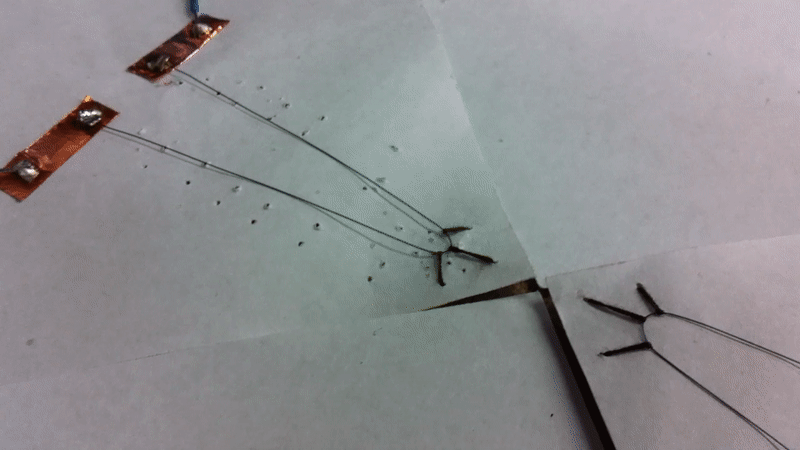
Finally, I began working on applying these techniques into a circuit itself. Thankfully, I have much more experience here than in the prior steps and was able to treat the SMA wires as a part of a regular circuit diagram that would attach to an arduino and 9V batteries for power.
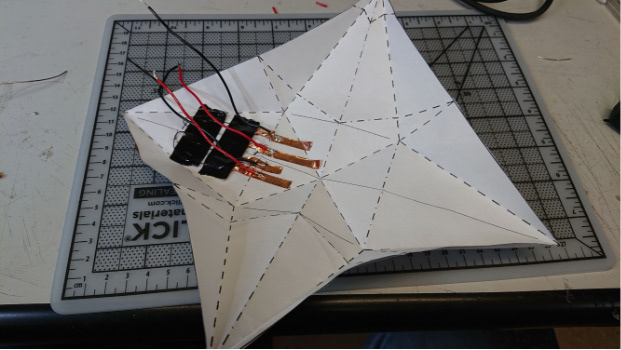
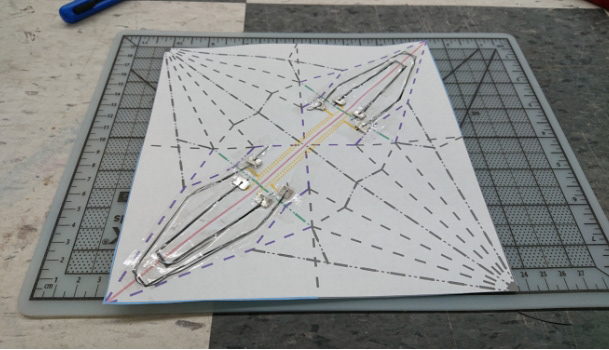
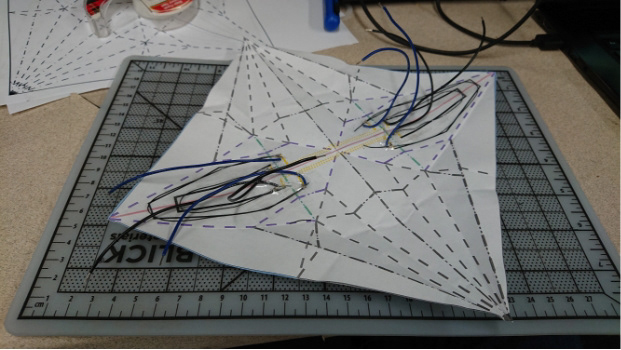
Final Design
Physical Design
Using the instructions I developed above, I created the final model of the origami crane. Using printer paper, SMA wire, copper tape, and an arduino, the crane will respond to touch and flap it's wings.
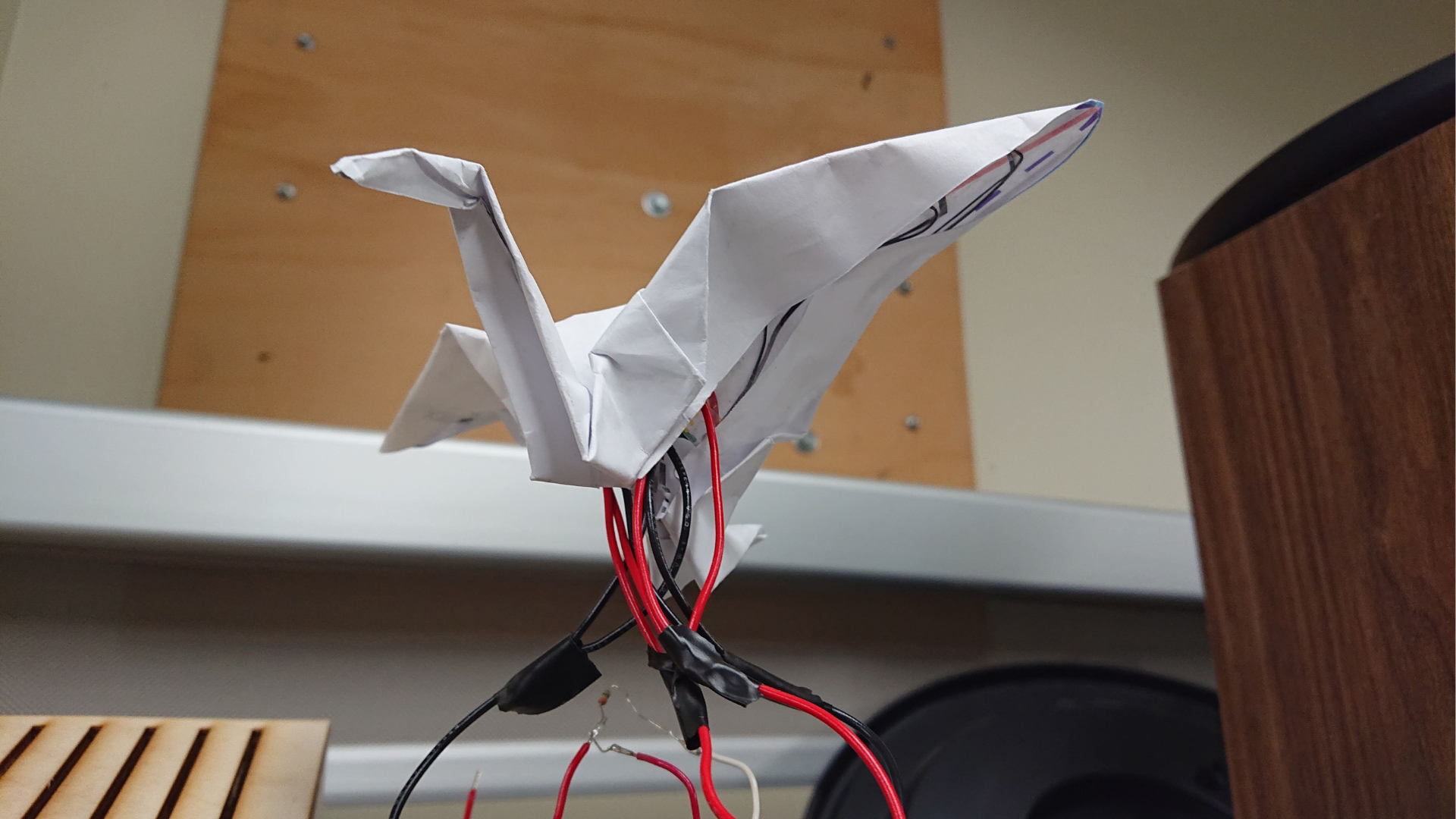
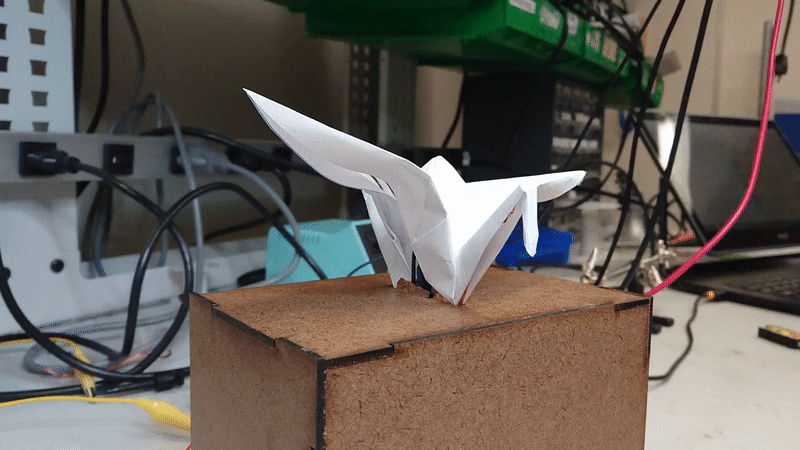
Digital Design
As a result of the process that I created while making this model, I was able to create a general manual for any origami piece. This allows will allow this product to be used by Akhil in the future with his Origami experience and creativity. These instructions are based off the existing crease patterns that normally exist in origami works and that experts use when documenting and iterating their designs.
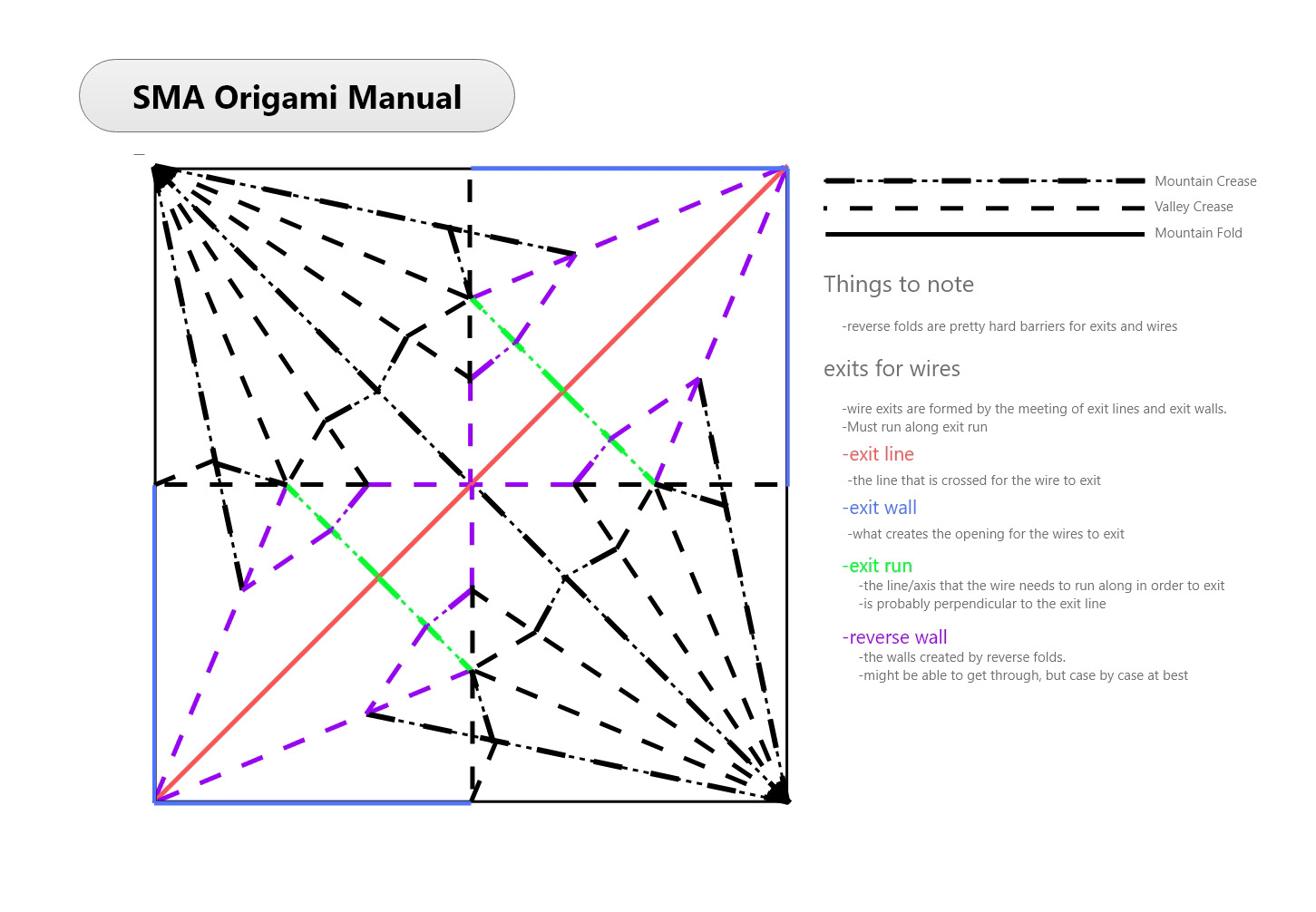
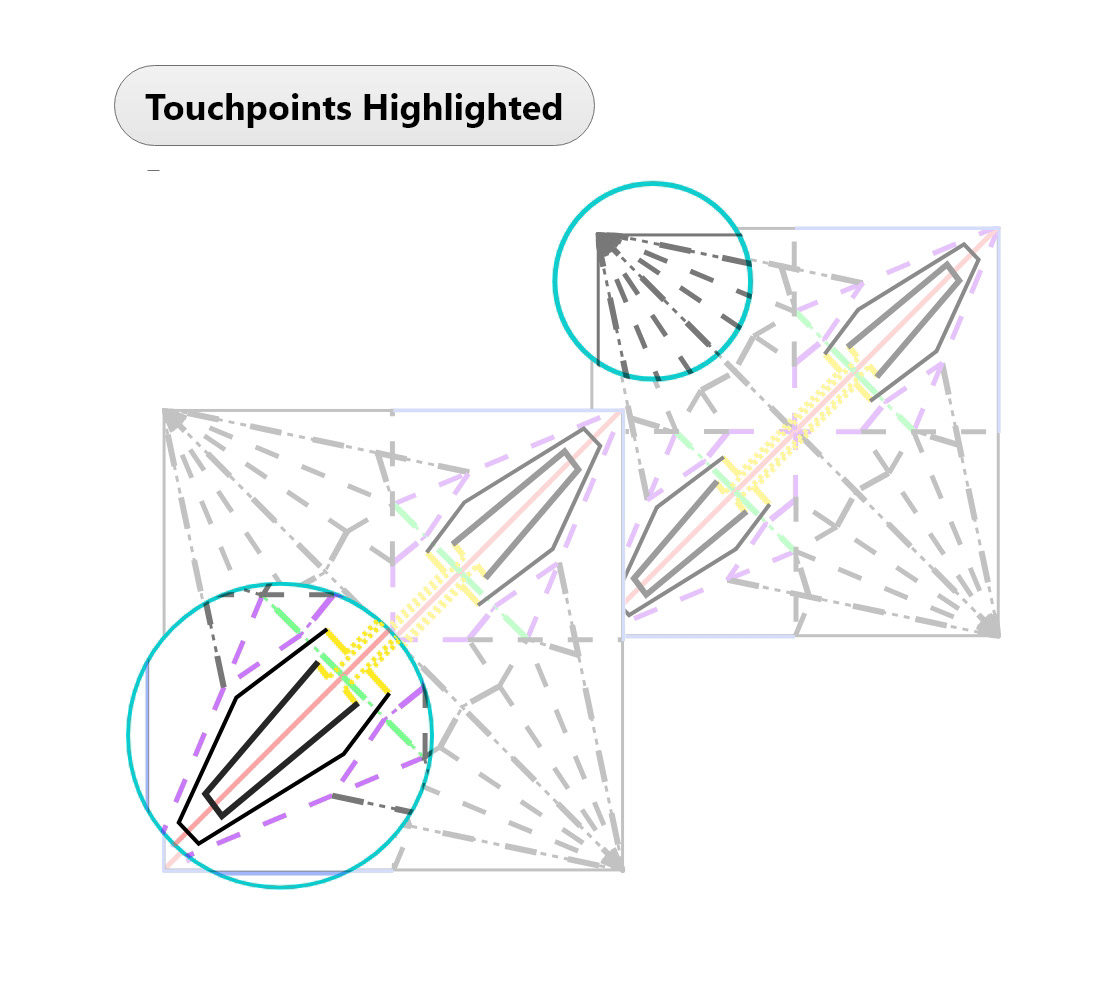
Looking Back
Despite the work done here, I realize the work I've done is only the tip of the iceberg with what can happen here. For example, there are so many other methods to creating a circuit, and perhaps software could be created to assist in the crease pattern generation. This isn't even looking at the other forms that could be created, and any future iterations would experiemtn with different forms and materials. I've done a lot of physical products in my time, but this was the most experimental project I have done, and probably the most fun I had. Despite the difficulties of learning a craft I had not practiced in years, the payoff of the playful interaction with the crane was entirely worth it. It was a great opportunity for me to practice designing for an individual and tailoring a solution for them specifically as well.
Fail Fast: With the amount of iteration I did in the protoyping phase of this project, I learned very quickly how to test certain aspects quickly without rebuilding the entire project each time. This is ultimately what led to a complete project by the end of the time period I had.